CHAPTER 6
QUALITY ASSURANCE
As you progress up the ladder of responsibility as
an Electronics Technician, you will become more
involved in the field of quality assurance (QA). As an
ET1 or ETC, you will be responsible for ensuring that
the work performed by your technicians and by
outside help is completed with the highest quality
possible. Most of the personnel in the ET rating take
pride in the performance of their jobs, and they
normally strive for excellence. However, every
individual has an occasional off day. For example,
your best technician may have had the midwatch the
previous night. When an individual is tired and not
100 percent alert, oversights or mistakes are easy to
make. One of your many responsibilities as the work
group or work center supervisor will be to ensure that
all corrective action performed is done correctly and
meets prescribed standards. Improper performance of
repairs or installations could endanger an expensive
piece of equipment or cause another piece of
equipment to fail prematurely. A well-organized QA
and inspection program will minimize the impact of a
moment of carelessness or inattention. In this chapter
we will familiarize you with the purpose, basic
organization, and mechanics of the quality assurance
(QA) program.
You may be assigned as a QA representative or
collateral duty inspector from time to time. As a work
center supervisor, you will be responsible for the
quality control program in your workspaces. It is
important that you become quality conscious. To
make any program successful, you will have to know
and understand the QA program and obtain the
cooperation and participation of all your personnel.
This requires you to ensure that all tests and repairs
conform to their prescribed standards. In addition,
you as a supervisor must train all of your personnel in
quality control (QC).
QUALITY ASSURANCE PROGRAM
The QA program was established to provide
personnel with information and guidance necessary to
administer a uniform policy of maintenance and repair
of ships and submarines. The QA program is intended
to impart discipline into the repair of equipment, safety
of personnel, and configuration control; thereby
enhancing the ships readiness.
The various QA manuals set forth minimum QA
requirements for both the surface fleet and the
submarine force. If more stringent requirements are
imposed by higher authority, such requirements take
precedence. If conflict exists between the QA manual
and previously issued letters and transmittals by the
appropriate force commander, the QA manual takes
precedence. Such conflicts should be reported to the
appropriate officials.
The instructions contained in the QA manual apply
to every ship and activity of the force. Although the
requirements apply primarily to the repair and
maintenance done by the force intermediate
maintenance activities (IMAs), they also apply to
maintenance done aboard ship by the ships force. In all
cases, specifications must be met. If specifications
cannot be met, a departure from specifications request
must be completed and reported. This will be discussed
later in the chapter.
Because of the wide range of ship types and
equipment and the varied resources available for
maintenance and repair, the instructions set forth in the
QA manual are necessarily general in nature. Each
activity must implement a QA program to meet the
intent of the QA manual. The goal should be to have all
repairs conform to QA specifications.
PROGRAM COMPONENTS
The basic thrust of the QA program is to ensure that
you comply with technical specifications during all
work on ships of both the surface force and the
submarine force. The key elements of the program are
as follows:
1.
2.
6-1
Administration. This includes training and
qualifying your personnel, monitoring and
auditing programs, and completing the QA
forms and records.
Job Execution. This includes preparing work
procedures, meeting controlled material
requirements, requisitioning material,
conducting in-process control of fabrication and
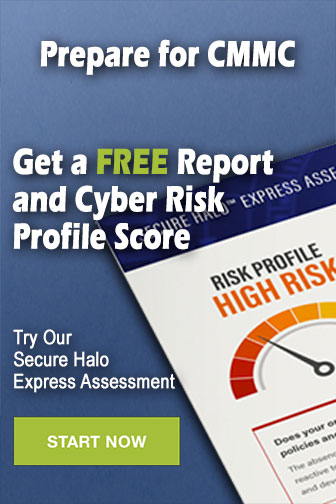