repairs, testing and recertifying, and
documenting any departure from specifications.
CONCEPTS OF QUALITY ASSURANCE
The ever-increasing technical complexity of
present-day surface ships and submarines has spawned
the need for special administrative and technical
procedures known collectively as the QA Program. The
programs concept is fundamentally the prevention of
defects. This encompasses all events from the start of
maintenance operations until their completion and is the
responsibility of all maintenance personnel.
Achievement of QA depends on preventing
maintenance problems through your knowledge and
special skills. As a supervisor, you must consider QA
requirements whenever you plan maintenance. The
fundamental rule for you to follow for all maintenance
is that TECHNICAL SPECIFICATIONS MUST BE
MET AT ALL TIMES.
Prevention is concerned with regulating events
rather than being regulated by them. It relies on
eliminating maintenance failures before the y happen.
This extends to safety of personnel, maintenance of
equipment, and virtually every aspect of the total
maintenance effort.
Knowledge is obtained from factual information.
Quality assurance knowledge is acquired through the
proper use of data collection and analysis programs. The
maintenance data collection system provides
maintenance managers with unlimited quantities of
factual information. Their correct use of this
information provides them with the knowledge required
to achieve maximum readiness of aircraft and weapon
systems.
Special skills, normally not possessed by
production personnel, are required by a staff of trained
personnel who analyze data and supervise QA
programs.
The QA program provides an efficient method for
gathering and maintaining information on the quality
characteristics of products and on the source and nature
of defects and their impact on the current operation. It
permits decisions to be based on facts rather than on
intuition or memory. It provides comparative data that
will be useful long after the details of particular times or
events have been forgotten. Quality assurance requires
that certain individuals have both the authority and the
responsibility for overseeing QA related actions.
A properly functioning QA program points out
problem areas to maintenance managers so they can take
appropriate action to accomplish the following:
1.
2.
3.
4.
5.
6.
7.
To
Improve the quality, uniformity, and reliability
of the total maintenance effort
Improve the work environment, tools, and
equipment used in the performance of
maintenance
Eliminate unnecessary man-hour and dollar
expenses
Improve the training, work habits, and
procedures of maintenance personnel
Increase the excellence and value of reports and
correspondence originated by the maintenance
activity
Distribute required technical information more
effectively
Establish realistic material and equipment
requirements in support of the maintenance
effort
obtain full benefits from a QA program,
teamwork must be achieved first. Blend QA functions
with the interest of the total organization and you
produce a more effective program. Allow each worker
and supervisor to use an optimum degree of judgment
in the course of assigned daily work; a persons
judgment plays an important part in the quality of his or
her work Quality assurance techniques supply each
person involved with a job with information concerning
actual product quality. This information provides a
challenge to the person to improve the quality of the
work. The resulting knowledge encourages the best
efforts of all your maintenance personnel.
Quality assurance is designed to serve both
management and production equally. Management is
served when QA monitors the complete maintenance
effort of the department, furnishes factual feedback of
discrepancies and deficiencies, and provides the action
necessary to improve the quality, reliability, and safety
of maintenance. Production is served by having the
benefit of collateral duty inspectors formally trained in
inspection procedures; it is also served in receiving
technical assistance in resolving production problems.
Production personnel are not relieved of their basic
responsibility y for quality work when you introduce QA
to the maintenance function. Instead, you increase their
responsibility by adding accountability. This
accountability is the essence of QA.
6-2
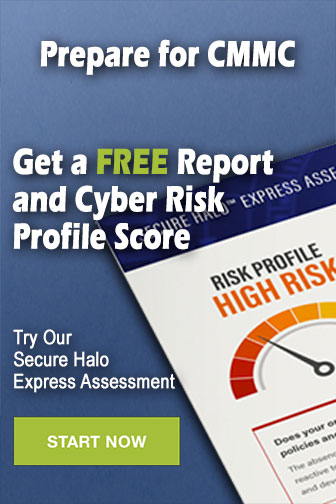