is used to pressurize the tank through a quick disconnect
or Schrader valve.
In other systems, a permanent pipe installation is
connected to the expansion tank through a
pressure-relief valve and an air shutoff valve. The ships
low-pressure air system is used to charge the pressure
tank, and then it is secured to prevent a possible
floodback of coolant into the low-pressure air system.
The relief valve is provided to protect the tank and
distilled water system from being overpressurized. The
sight glass and the low-level alarm switch function the
same as those on the gravity expansion tank.
In both types of expansion tanks, the bottom of the
tank is connected by piping to the return main of the
secondary cooling system (fig. 1-6). Changes in coolant
volume causes the coolant to flow into or out of the
reservoir as necessary to maintain a stable, liquid
coolant, return-line pressure.
Makeup water (distilled water) is added to the
expansion tank through the funnel located on the top of
the tank (fig. 1-11 and 1-12). A funnel cap is provided
for the funnel to prevent dirt from entering the system
through the funnel. Whenever you fill the pressurized
expansion tank, you have to first isolate the tank from
the cooling system and the air supply, then vent the air
pressure off through the vent pipe located at the top of
the tank. The makeup water can be obtained directly
from the ships evaporators and preferably when the
ship is making boiler feed water, because the water is
double distilled. At NO time should potable (drinking)
water or treated boiler feed water be used in any
electronic cooling systems. After the water is drawn
from the ships evaporators, it should be transported
using only a clean capped container. You should take a
sample of the water from the containers and have it
tested for chloride by the ships water test facility before
any of the water is used in the cooling system. The
maximum permissible level of chloride is .065 epm
(equivalent parts per million). The supply system
provides an alternate source of makeup water.
The expansion-tank sight glass is your best
indication of a coolant leak in the secondary cooling
system. When the system uses excessive makeup water,
you should inspect the whole secondary system,
including the telltale drains on the heat exchanger, to
locate the source of the leak. A small drip can amount
to several gallons of water a day. On the pressurized
expansion tank, a very small air leak indicated by a
pressure drop on a tank gauge can be located by brushing
on a leak detector (a thick, clear, soapy liquid such as
concentrated liquid dishwasher soap) over the suspected
area of the leak. The escaping air causes bubbles to form
in the leak detector.
SEAWATER STRAINERS
Strainers are used in the seawater cooling system to
remove debris and sea life, which could clog the
pressure and flow control device (orifice) and/or the
tubes of the heat exchanger. The two types of in-line
seawater strainers most commonly used in weapons
cooling systems are the simplex (single) and duplex
(double) basket strainers.
The simplex basket strainer (fig. 1-13) consists of a
Y-pattern body housing a wire mesh basket. Some
simplex strainers have a small drain on the cover to
allow you to drain the water off before removing the
cover. The basket is removed periodically for cleaning
and inspecting for deterioration. This type of strainer
requires that the seawater be secured before you clean
the basket.
Figure 1-13.-Seawater simplex strainer.
1-11
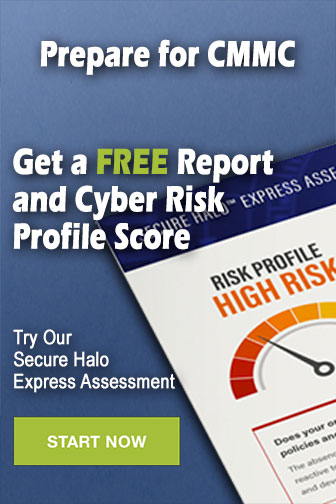