Figure 1-22.-Venturi flowmeter.
differential pressure (pressure drop) is sufficient, the
microswitch will activate to indicate that the switch has
the proper flow through it. You should be sure that the
flow switch is defective before overhauling or replacing
it. The problem could be a partially closed supply/return
valve, obstruction in the coolant line, insufficient
coolant pressure, or many other things. By using the
coolant system pressure gauges and/or the installation
of a permanent or a temporary in-line flowmeter, you
should be able to correctly isolate the problem.
In the secondary cooling system, a full-flow system
flowmeter (figs. 1-6, 1-7, and 1-8) is provided to enable
you to monitor the total system flow rate for
troubleshooting purposes. There are three types of
system flowmeters installed aboard ship. All of them
serve the same functional purpose of monitoring coolant
flow rate.
You will encounter the venturi-type
flowmeter, orifice-type flowmeter, and the rotameter
flowmeter. Most systems incorporate one secondary
coolant flowmeter and one or more smaller flowmeters
to ensure that the electronic equipment is being supplied
with an adequate flow of coolant.
In the venturi-type flowmeter (fig. 1-22), as the
coolant approaches the contracted portion (throat) of the
meter, its velocity must increase as it flows through the
contracted zone. The angle of approach is such that no
turbulence is introduced into the stream. A pressure tap
is located at the side wall in the pipe ahead of the meter,
and another one is located at the throat. The increase in
velocity of the coolant water through the throat results
in a lower pressure at the throat. The flow rate is
proportional to the difference in pressure between the
two taps. The gradual tapering of the meter walls back
to pipe size downstream of the throat allows the coolant
water to slowdown with a minimum of lost energy. This
allows a recovery of nearly 99 percent of the pressure
on the approach side.
To monitor the amount of flow through the
venturi-type flowmeter, a differential pressure gauge is
used to monitor the pressure difference between the two
pressure taps. A calibration chart is usually supplied
with the flowmeter to convert the differential pressure
to gallons per minute (gpm), or the face of the meter may
indicate readings in gpm.
The orifice flowmeter works in the same manner as
the venturi flowmeter, but its construction is much
simpler and less expensive to manufacture. In place of
the tapered throat, the orifice flowmeter uses a flat plate
with a hole in it, which causes a considerable loss of
pressure downstream. The efficiency of this type of
flowmeter can be as low as 65 percent.
The rotameter (fig. 1-23) is a variable area orifice
meter that functions by maintaining a constant
differential pressure with varying flow. The rotameter
consists of a float positioned inside a tapered, tempered
glass tube by the action of the distilled water flowing up
Figure 1-23.Rotameter.
1-18
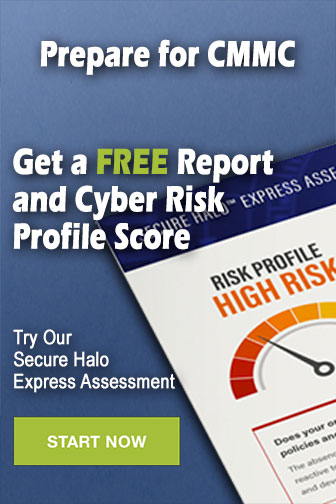