PERSONNEL ORIENTATION
The best way to get the support of your personnel is
to show them how an effective QA program will benefit
them personally. Eliminating or reducing premature
failures in repaired units and introducing high-reliability
repairs will appreciable y reduce their workload, saving
them frustration and enhancing the shops or work
groups reputation. This program, as with any new
program or change to an existing program, will probably
meet with opposition from some shop personnel. By
showing your shop personnel the benefits of a QA
program, you greatly reduce opposition to the change.
REPAIR PROCEDURES
Repair procedures may be defined as all of the
action required to return an equipment to its proper
operating condition after a defect has been discovered.
Repair procedures include parts handling, disassembly,
component removal or replacement, and assembly.
Strictly adhering to the proper repair procedures will
almost entirely eliminate premature failures. You, as
shop supervisor or work group supervisor, and
subordinate work center supervisors are responsible for
ensuring that the proper procedures are used in handling
all repairable units.
QUALITY ASSURANCE TERMS
AND DEFINITIONS
As a supervisor, you need to be able to talk to your
personnel about quality assurance and have them be able
to carry out your instructions promptly and properly.
You need to promote the use of words and phrases
pertaining to quality and related programs, thus
improving the clarity in your communication with them
about QA. To do this, you need to understand the terms
frequently used throughout the QA program. Each
TYCOMs QA manuals and MIL-STD-109 have a
complete list of these terms, but the most frequently used
terms are listed here:
Quality assurance. Quality assurance (QA) is a
system that ensures that materials, data, supplies,
and services conform to technical requirements
and that repaired equipments perform
satisfactorily.
Quality control. Quality control (QC) is a
management function that attempts to eliminate
defective products, whether they are produced or
procured.
Acceptance. Acceptance is when an authorized
representative approves specific serves rendered
(such as a repair or manufactured part).
Calibration. This is the comparison of two
instruments or measuring devices, one of which
is a standard of known accuracy traceable to
national standards, to detect, correlate, report, or
eliminate by adjustment any discrepancy in
accuracy of the instrument or measuring device
being compared with the standard.
Inspection. This is the examination and testing
of components and services to determine
whether they conform to specified requirements.
In-process inspection. This type of inspection is
performed during the manufacture and repair
cycle to prevent production defects. It is also
performed to identify production problems or
material defects that are not detectable when the
job is complete.
Inspection record. Inspection records contain
data resulting from inspection actions.
Specifications. A specification is any technical
or administrative directive, such as an
instruction, a technical manual, a drawing, a plan,
or a publication, that defines repair criteria.
Audit. An audit, as it applies to the QA program,
is a periodic or special evaluation of details,
plans, policies, procedures, products, directives,
and records necessary to determine compliance
with existing requirements.
Certified (Level I) material. This is material
that has been certified (as to its material and
physical properties, as well as traceability to the
manufacturer) by a qualified certification
activity. This material has a material and
identification control (MIC) number assigned
along with a certification document.
Controlled material. This is any material that
must be accounted for and identified throughout
the manufacturing or repair process. (See level of
essentiality).
Controlled work package. A controlled work
package (CWP) is an assemblage of documents
identified by a unique serial number that may
contain detailed work procedures, purchase
documents, receipt inspection reports, objective
quality evidence, local test results, and any tags,
6-8
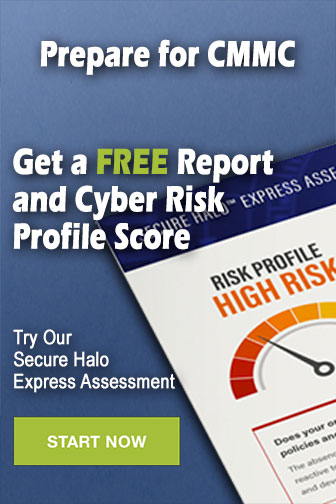