fixed orifice (B) in the valve body for this purpose. It
is expanded to atmospheric pressure through the fixed
orifice, which controls the purge airflow. The purge air
back flows to atmosphere through each desiccant
chamber during half of each cycle. The dry purge air
enters the top of the chamber. The oil and water that are
removed from the chamber are discharged from the
bottom of the chamber through the purge muffler.
The key to the simplicity and unusual efficiency of
the dehydrator is its unique valving system. A particular
point to notice is that the solenoid control valves handle
only the purged air. (The main airflow through the unit
does not pass through them as in older units employing
three-way valves.) This means that simple,
direct-acting, large-orifice, two-way valves can be used
to eliminate the sources of high-pressure drops. In
addition, this type of valve is more dependable.
Let us take a detailed look at the operation of a
dehydrator. Well consider a complete cycle of
operation. Refer to figure 2-6, phases I, 11, and III for
the following descriptions.
PHASE IDRY/PURGE. The solenoid valve
(F) is closed. Solenoid valve (D) is open. Incoming
moist air, under pressure, flows through chamber (A),
where it is dried. Most of this dry air is passed through
the outlet conduit to be put to use. A small quantity,
however, bypasses the closed ball-check valve (E)
through a small orifice (B) into chamber (C). Here it
picks up moisture from the partially saturated desiccant
and passes out of the unit through the open valve (D).
Since the chamber being purged is at near-atmospheric
pressure, the ball-check valves (E) and (G) are held in
place by the pressure of the main airflow.
PHASE IIDWELL. The timer closes both
solenoid valves (D) and (F). This allows the pressure in
the regenerated chamber (C) to build up through the
orifice to approximately that of chamber A.
PHASE IIIDRY/PURGE. In figure 2-6
(phase III), the solenoid valve (F) is opened by the timer;
solenoid valve (D) remains closed. The pressure in
chamber (A) drops immediately, causing the ball-check
valves (E) and (G) to move rapidly to the right, sealing
off chamber (A) and directing the main airflow through
chamber (C) where it is dried. A portion of this dry air,
leaking through orifice (H), passes through chamber(A)
where it picks up moisture and is emitted to the
atmosphere through valve (F). After completing
another dwell period, the cycle repeats.
The most important single aspect of maintaining the
dehydrator is to assure proper operation of the automatic
dump traps on the fluid separator and the telltale oil filter
units. If oil, water, and sludge are not expelled the
accumulated liquids may fill the trap, back up into the
air lines, and pass into the dehydrator. Complete failure
of the desiccant material of the dehydrator to dry and
purify quickly follows. If this happens, you will have
to completely disassemble and clean the fluid separator,
telltale oil filter, both dump traps, the pressure regulator,
the dehydrator, and all the interconnecting piping. Also,
the desiccant in the dehydrator chambers will have to be
replaced.
Dust Filter
The dust filter (fig. 2-1) consists of a separable
housing, which contains a replaceable falter cartridge,
constructed of pleated paper (5 microns). The design is
such that air flows from the outer (housing) side inward
to a hollow center that is connected to the outlet port.
Dust is then collected on the outer surface of the filter
cartridge. Since the collected dust is dry, any substantial
accumulation falls to the bottom of the housing and
lessens the possibility of clogging the filter.
Flow Limiter
A flow limiter (fig. 2-1) is installed between the dust
filter and output of the dryer. It is designed to limit the
output of the dryer, should the output of air increase
beyond the limits of the dryer capability.
The flow limiter is a spring-restrained poppet valve
with an orifice in the poppet valve. The poppet valve
offers no appreciable resistance to the flow of air during
normal operation. When the flow exceeds the design of
the dryer, the poppet valve closes, and the flow is then
limited by the orifice in the poppet valve.
MOISTURE MONITOR
A moisture monitor probe is installed downstream
from the dryer to monitor the dew point of the dry air.
The monitor gives you a visual reading in ppm (parts
per million) or in dew point (for example, 40°F). Most
monitors have a built-in alarm system. It provides both
audible and visual alarms when the air quality is less
than the value that it is set to.
When the monitor unit is designed to read the
moisture content of the air in dew point, a conversion
chart is included with the unit. This chart converts the
individual reading to a standard dew-point reading,
which is at atmospheric pressure; for example, a dryer
feeding three waveguide systems at 10, 20, and 30 psig.
2-8
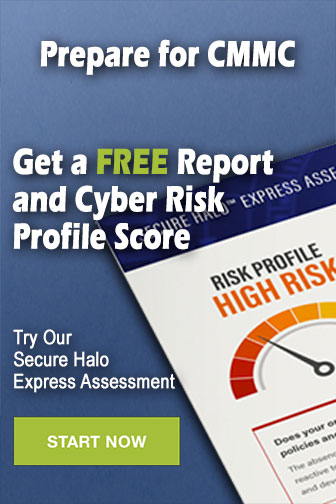