unit. The controller selects the desired head and direct
seeks the read/write head assemblies to the selected
cylinder position.
During a write operation, data is
output from the controller buffer memory to the disk
write circuitry and recorded on the disk using the
modified frequency modulation (MFM) encoding
method. Modified frequency modulation encoding is
covered in detail later in this chapter. During a read
operation the drive recovers data from the disk and
transfers it to the controller.
The disk drive uses a motor driven belt and pulley
arrangement to rotate the mounted disk pack at a speed
of 3,600 rpm ±3.5%. The speed of disk pack rotation
is monitored by a spur gear and photocell arrangement.
The read/write heads, five addressable read/write
heads, and one read-only head (servo head) are mounted
on arm assemblies controlled by an actuator assembly.
The disk pack must be rotating above 3,100 rpm before
the actuator assembly will load the heads or move them
over the recording surfaces. The heads are designed to
float above the disk pack recording surfaces on the air
cushion provided by the high-speed rotation. Any
contact between the read/write heads and the disk
recording surfaces will result in a head crash and
damage to both heads and recording surfaces. The
heads are automatically unloaded or retracted if the
drive motor power is turned off or the rotation speed of
the disk pack drops below 3,100 rpm.
The movement of the read/write heads to the
desired cylinder position is controlled by a closed-loop
servo system. Prerecorded data written on the servo
surface is used to (1) determine the present position of
the read/write heads, (2) control the movement of the
read/write heads when seeking a new cylinder, and (3)
maintain alignment of the heads to the tracks on the
recording surfaces when data is being read or written.
The disk drive is divided into the following
electronic and electromechanical assemblies and
functional areas:
Drive motor assembly
Spindle assembly
Speed sensor
Actuator assembly
Velocity transducer
Head/arm assemblies
servo circuit
l Track servo circuit
l Read/write circuits
Drive Motor Assembly
The drive motor, which drives the spindle assembly,
is a 1/2-horsepower induction motor. Power is
transferred to the spindle via a flat, smooth surfaced belt
that connects the pulleys of the spindle and drive motor.
The speed of the drive motor is sensed by an optical
switch and controlled by the motor supply module in
the power supply.
Spindle Assembly
The spindle assembly is the physical interface
between the disk drive and the disk pack. The surface
of the disk pack mounting plate on the spindle mates
directly with the center of the disk pack. Mating
surfaces of the disk pack and spindle are engaged by
rotating the cover handle of the disk pack when you
install the pack in the drive. When the pack and the
spindle are fully engaged, the canister cover is released
from the disk pack. You can then remove the cover.
The spindle is driven by the drive belt, which
connects the spindle to the drive motor pulley. A static
ground spring is mounted at the lower end of the spindle
assembly to protect against the buildup of a static
charge. A spur gear is mounted on the lower end of the
spindle drive shaft. The teeth of the gear pass through
the optical switch and are used as part of the speed
sensor.
Speed Sensor
The speed sensor monitors and controls the rotating
speed of the spindle and its attached disk pack. The
speed sensor is made up of the spur gear and the speed
sensor photocell in the optical switch. The teeth of the
spur gear pass through and interrupt the light path
between the emitter lamp and photocell. The pulsed
output generated by the speed sensor is sent to the power
supply module. The power supply varies the drive
motor current to control the speed of the drive motor
and to maintain spindle speed within the required limits.
Actuator Assembly
The actuator assembly is the mechanism that
supports and moves the head/arm assemblies. The
actuator is made up of a carriage and voice coil
10-20
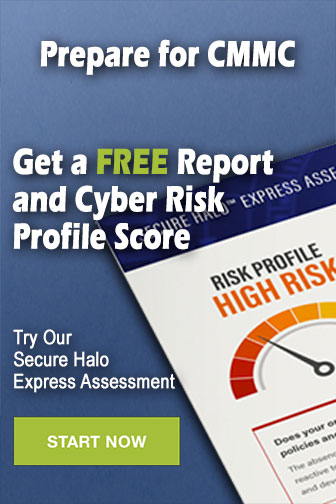