ET rating; your shop will normally have several of
these NEC requirements. At the present time, almost
all ETs are assigned, by the Bureau of Naval Personnel
(BUPERS), according to the requirements of the
NECs.
Shop personnel are the key to your success as a shop
supervisor. Without their continuing loyalty to you and
their willingness to follow in the direction that you lead,
you will be unable to effectively achieve the required
results. You may be a good technician; but remember,
you cannot do everything yourself.
MATERIAL ASSETS
Basically, your material assets are every material
thing, such as parts, tools, test equipment, and work
space, that you need to perform the shops maintenance
role. A deficiency in any one area makes it difficult for
you to perform your job in the most efficient manner.
By carefully surveying your shop and identifying its
shortcomings, you can take corrective action and
improve the conditions under which your shop
personnel will be working.
ADEQUACY OF SPACES
Sometimes it seems as if electronics spaces are
designed by people who will never have to use them for
maintenance. Ashore, the facilities are normally
adequate to provide proper maintenance. However,
aboard ship there is little space that is not dedicated to
some other vital function.
As a shop supervisor you may feel there is little you
can do about the inadequacies of your shop spaces.
Sometimes this may be true; but, in most cases, if you
analyze carefully and do some brainstorming, you can
devise better methods of arranging the workspace. This,
in turn, should result in more efficient working
conditions. Consider each shop on a case-by-case basis.
Brackets, stowage bins, book shelves, and collapsible
workbenches can be installed in an amazing number of
places that previously may have been overlooked. Get
all of your people in on the planning. They will be more
likely to excel when they play a vital part in fixing up
the shop.
If you are fortunate enough to be in on the planning
stages of a maintenance shop, there are a number of
things that you should consider:
. Is adequate lighting available?
l
l
l
l
Are adequate 60-Hz and 400-Hz (if applicable)
power receptacles available?
Is the layout of the shop the most effective use of
the space?
Are special safety devices or safety precautions
needed in the shop area?
If parts storage is included, is it centrally
located to all work stations as practically as
possible?
These are just a few of the questions that you
will be asking. The only limits to how well a shop
can meet your needs are the space available and
your ingenuity and imagination. If space is
available, you should be able to develop the plans
for an efficient work area.
MATERIAL AVAILABILITY
Material availability determines how long it takes
to complete a maintenance action. A spare part for a
particular piece of equipment could require from 6
months to over a year to acquire from a vendor who
has to produce it on a special order. There is little the
shop supervisor can do about this situation. There are
many other situations, however, in which the shop
supervisor can play a controlling role. Consider a few
of the materials that are under the control of the
supervisor:
Tools
Test equipment
Consumables
Safety equipment
Other materials specific to your shop
Respect your personnel by having the correct
material available so they can perform their preventive
and corrective maintenance without delays caused by
lack of material.
CONTROL OF MATERIAL ASSETS
The most effective way to control material assets
is to maintain some form of accountability. Mass
issuing of tools to all shop personnel represents a
major expense, and it usually means the tools will
not be available when needed. Loaning test
equipment items to every work center that wants to
borrow them may mean the equipment will not be
3-13
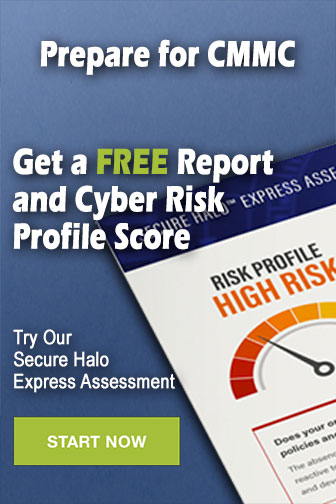