CHAPTER 1
LIQUID COOLING SYSTEMS
Liquid cooling systems are vital to the proper
operation of shipboard electronic equipment. Because
of their importance, these cooling systems must be
reliable and readily available. Study the contents of this
chapter carefully. The knowledge you acquire may one
day help you prevent heat damage to a multimillion
dollar piece of equipment and the loss of countless
manhours being expended in its repair. Imagine how
you would feel if the damage occurred because you had
not checked a temperature gauge at a particular time
because you were not aware of its purpose or existence.
Knowledge of the equipment is one of the greatest
safeguards that you can develop. Let us begin by
discussing the methods for cooling electronic
equipments and systems.
ELECTRONIC EQUIPMENT
COOLING METHODS
Most electronic equipment generates sufficient heat
so that some form of equipment cooling is required
during normal operation. Heat is generated by various
parts of the equipment because electrical energy is
dissipated in the form of heat whenever current flows
through a resistance. This heat must be removed to
prevent a change in the equipments operating
parameters and to prevent possible breakdown of
electronic parts.
This section on liquid cooling systems describes
some of the more common methods of heat removal
from electronic equipment. It provides the basic
knowledge necessary for better understanding of the
major components, operation, and maintenance of a
typical cooling system. Our discussion will highlight
four methods of cooling: convection, forced-air,
air-to-air, and air-to-liquid.
CONVECTION COOLING
Cooling by the convection principle is shown in
figure 1-1. As the heat of an equipment part warms the
air in its vicinity, the warm air, being lighter, rises
through the outlet openings. The cooler air is drawn in
through the inlet openings to replace the warm air. This
method is limited in its cooling effect because it relies
Figure 1-1.-Convection cooling.
upon the natural airflow and requires that the equipment
enclosure be of open construction without air falters.
To increase heat dissipation, a finned heat sink can
be added to the heat-producing part, as shown in figure
1-2. The fins increase the effective surface area of the
part, allowing more heat to be transferred to the air. For
the maximum transfer of heat, the part must make
contact with the heat sink. Silicone grease is usually
applied between the heat source and heat sink for better
thermotransfer. The heat sink must be kept free of any
dirt or dust, which would act as an insulator.
Figure 1-2.Finned best sink.
1-1
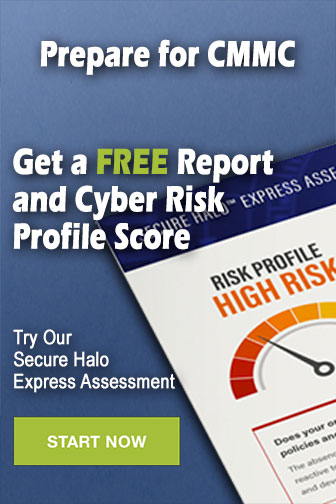