rotor is geared to its mechanical input and one rotation
of the input results in one revolution of the transmitters
rotor. The speed of a synchro transmitter is tied to the
gear ratio between the mechanical input to the
transmitter and the transmitters rotor; that is, 1:1, 36:1,
and so on.
In a 36-speed synchro system, the rotor of the
synchro transmitter is geared to rotate 36 times for one
revolution of the input shaft (36:1). Units transmitting
data at one speed (l-speed, 36-speed, and so forth) are
called single-speed synchros. The entire range of data
to be transmitted is contained in the output of the
single-synchro transmitter.
It is quite common for shipboard synchro systems
to transmit data using two different speed synchros with
the same reference or supply voltage. For example,
ships course (ownships heading) information is
usually transmitted to other locations using a 1-speed
synchro and a 36-speed synchro. A synchro system that
transmits data using two different speed synchros is
called a dual-speed synchro system or a double-speed
synchro system.
COARSE AND FINE DATA TRANSMIS-
SION. Dual-speed synchro transmissions are
combined to improve the accuracy of the data
transmitted. The use of two transmitting synchros
allows for a coarse value and a fine value to be sent at
the same time. The synchro with the lowest ratio (1:1)
sends the coarse value. The synchro with the highest
ratio (36: 1) sends the fine value. The coarse and fine
values transmitted can be likened to the hour and minute
hands of a clock. The course value represents the time
in hours. The fine value represents the time in minutes.
The two values must be combined to give the time in
hours and minutes.
Lets look at a coarse synchro and a fine synchro
transmitting an angular position such as ships course
(ownships heading), which can be from 0 degrees to
359 degrees true. The coarse synchro (1:1) indicates
360 degrees of ships course with one rotation.
However, the accuracy of the data is limited to plus or
minus 1 degree of heading. This degree of accuracy is
not enough for most navigation systems to keep an
accurate track of ships movement. The fine synchro
(36:1) rotates 36 times for each rotation of the coarse
synchro. This means the fine synchro rotates once each
10 degrees (360/36). Within its 10-degree segment, the
fine synchro is 36 times as accurate as the coarse
synchro. The use of dual-speed synchros requires two
S/D conversions to take place; one to determine the
position of the rotor in the coarse synchro transmitter
and one to determine the position of the rotor in the fine
synchro transmitter.
SYNCHRO SIGNALS. A single-speed synchro
transmitter outputs three waveforms that indicate the
angular position of the rotor in the transmitting synchro,
for example a control transmitter (CX). Waveforms are
induced in the stator coils by the magnetic field of the
rotor coil. The two rotor connections of the CX (R1 and
R2) are fed from a 115-volt ac supply voltage (also
called the reference voltage). This voltage is also fed
to the synchro-to-digital (S/D) converter circuitry. The
reference voltage is important in the conversion
process. It provides a reference for the S/D converter
to use when sampling the stator voltages.
The amplitude of the voltage output between the
stators (S1 to S2, S1 to S3, and S2 to S3) at any instant
is dependent on the position of the rotor in the CX. The
115-volt supply voltage induces an ac voltage into the
stator windings. The phase relationship of the signals
induced on each stator winding is dependent on the
angular position of the rotor within the CX. The rotor
can normally be rotated 360 degrees within the synchro.
The range of values being transmitted is tied to this 360
degree rotation.
The minimum value is normally
transmitted with the rotor at the 0-degree position and
the maximum value is sent when the rotor is positioned
to approximately 359 degrees.
All three stator signals are ac voltages that have the
same characteristics (frequency and amplitude). They
have a 120-degree phase difference (phase
displacement) from each other due to the 120-degree
separation of the wye windings of the stator coils in the
synchro transmitter. At any instant, a phase relationship
exists between the rotor supply (excitation) voltage and
the three stator voltages. This phase relationship is the
key to the S/D conversion process.
Basically, the phase relationship of the individual
stator voltages, across terminals S1, S2, and S3, varies
with the rotor supply voltage (R1-R2) as the rotor is
rotated within the synchro transmitter. Each position of
the rotor has a unique stator voltage phase relationship
to the supply (reference) voltage. At any instant, the
amplitude and polarity of the stator signals when
compared to the supply voltage indicate the angular
position of the rotor.
For dual-speed synchro systems, two sets of stator
voltages are transmitted, one set for the coarse synchro
and one set for the fine synchro. A single supply
voltage (reference) is used for both synchro
13-6
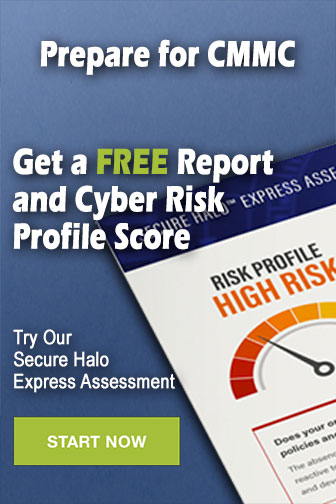