discrepancies caused by the shipper. Included in this
category are shortages, unacceptable overshipments,
unacceptable substitutes, material shipped in error,
shipment of wrong items, and missing or improperly
prepared supply documentation. Also included are
shelf-life items that were too old at the time of issue or
were issued with insufficient shelf-life remaining. A
QDR reports defective material that is not suitable for
its intended use because of a deficiency in design,
material, or procurement. These deficiencies can
include chemical, electrical, functional, or physical
discrepancies that occurred because the contractor did
not meet contractual or specification requirements. It
may also include deficiencies that resulted because the
contractual requirements (including the procurement
document that describes the technical requirements of
the material) were ambiguous, improper, incorrect, or
omitted. The QDR is reported to the Fleet Material
Support Office (FMSO); the ROD is reported directly
to the Navy stock point that issued and shipped the
material.
Survey Reports
A survey is the procedure required by U.S. Navy
regulations when naval property must be condemned
due to damage, obsolescence, or deterioration; or
acknowledged as nonexistent due to loss, theft, or total
destruction. The survey is performed according to
N4VSUP P-485.
Additional Reports
There are many other reports not mentioned in this
chapter; for example, the reports required by type
commanders and other authorities.
To increase the effectiveness of recurring reports
and to avoid duplication, the Navy instituted the Reports
Control Program. This program is used in the various
naval commands and offices, in the Marine Corps, in
each continental naval area, and in selected major field
activities. Direct responsibility for the program is vested
in the Chief of Naval Operations (OP 09B83).
RECORDS
Certain records are necessary to assist electronics
personnel in keeping up-to-date information on
equipment for which they are responsible.
As an electronics supervisor, you must ensure that
all of your required records are maintained properly. To
do this you should keep file copies of required reports.
In addition, you should maintain files on the following
topics:
Equipment
System
Safety
Inspections
Pre- or post-overhaul
3-M Systems
Personnel
The above list is not a complete list, but should give
you an idea of the type of records that you should
maintain. Have the records filed neatly and in an orderly
sequence. Purge them of any information that is not
required or will not be needed for reference. For
example, throw away 3-year-old information that is no
longer applicable.
Regulations concerning the use of records and
instructions are contained in the following references:
Naval Ships Technical Manual, chapters 090
and 400
NAVSEA
SE000-00-EIM-100
(formerly
NAVSEA 0967-LP-000-0100), Electronics
Installation and Maintenance Book, General
OPNAVINST 4790.4, Ships Maintenance and
Material Management (3-M) Manual
Type commanders instructions on required
records and command inspection guides
CORRESPONDENCE CONTROL
A method of keeping track of correspondence and
of routing information is important to any maintenance
shop. Over a period of a week a large amount of
correspondence enters and leaves the average work
center. Some of this correspondence requires action,
while some contains information for work center
personnel. Ensuring that information is routed to the
personnel of your work centers can be either a major
chore or a simple everyday task. No simple procedures
can help you simplify the job of keeping track of your
correspondence:
1. Routing procedures
2. Correspondence tickler file
2-5
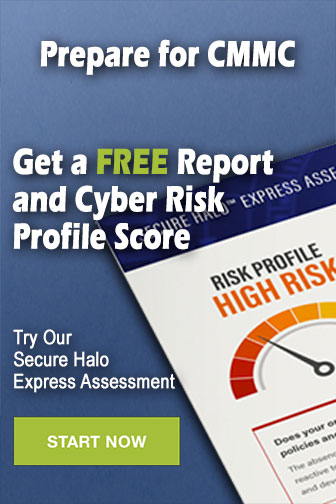