A double-pass heat exchanger is generally used
ensure that tools, such as screwdrivers and wire brushes,
when there is limitation on the installation of the heat
are not used in such a way that they may scratch or mar
exchanger. This type of heat exchanger is less efficient
the tube surfaces.
than a single-pass exchanger and is subject to internal
undetectable leakage across the flow divider in the
Over a period of time, electrolysis, which results
inlet-outlet water box.
because of dissimilar metals in the cooling system, will
slowly dissolve the insides of various components in the
It is to your advantage to maintain a log on the
performance of the heat exchangers installed in the
cooling systems with which you are involved. By
recording the operating characteristics, you will have
the data you will need to later analyze the performance
of the heat exchanger. The performance is monitored
by observing the temperature gradient (AT) between the
inlets and outlets of the two fluids. The overall
effectiveness of a heat exchanger is determined by
comparing its primary inlet temperature to its secondary
outlet temperature. For example, with no change in the
primary or secondary flow and if the heat transfer
capacity of the heat exchanger drops, the AT will
increase.
By comparing the AT readings taken
periodically with the clean heat exchanger AT readings,
you can detect the deterioration of a heat exchanger
because of fouling. By maintaining a record of both
input and output pressure gradient
you will be able
to determine which side of the heat exchanger is fouled.
Heat exchangers must periodically be cleaned. The
secondary section (distilled water) is cleaned by
circulating chemicals through the secondary cooling
system to remove any buildup of scale deposits, which
accumulate on the surface of the tubes. The procedure
for routine cleaning of the primary section of the heat
exchanger is to first secure the sea connections to
prevent flooding. In some cases, an inspection port in
the water box can be opened to remove any foreign
matter lodged inside and against the tubes. If you are
unable to get at the ends of the heat exchanger to remove
the water boxes, then you must remove the heat
exchanger from its location and place it on the deck or
a suitable work surface. Mark each unit removed so that
it can be positioned in its proper place during
reassembly. With the water boxes removed, an air lance
should be passed through each tube and the passages
washed out. Where severe fouling exists, a water lance
should be pushed through each tube to remove foreign
matter attached to the tube walls. Where extreme
fouling exists, special cleaning equipment operated by
personnel skilled in their use is required. The ships
engineering officer is the best person qualified to
determine which procedure to use and whether the job
can be performed aboard ship or if it must be transferred
to a repair facility.
You should take precautions to
primary seawater cooling system. (Electrolysis is not a
problem in chilled water systems to the extent that it is
in seawater systems.) The type of metal used in the
fabrication of the heat exchanger tubes is the deciding
factor as to the use of zincs anodes or zincs. Zincs are
disks, rods, bars, or plates made of zinc metal that are
installed inside the heat exchangers water boxes. When
zincs are installed, the electrolytic action is concentrated
on the zinc and not on the metal of the heat exchanger
tubes. As electrolysis dissolves the zincs instead of the
heat exchanger tubes, they should be replaced. (The
purity of distilled water inhibits electrolysis in the
secondary system.) In an older cooling system, you
should be on the lookout for thin pipes in the seawater
side of the cooling system. You can check forbad pipes
by gently tapping the empty pipes with the ball of a
ball-peen hammer. A bad piece of pipe will make a dull
sound and dimple as it is struck lightly. This work
should be scheduled for overhaul while the ship is
inport.
The heat exchangers in the distilled water cooling
systems that cool electronic equipment are either
liquid-to-air or coolant-jacket type of heat exchangers.
The liquid-to-air heat exchangers are mounted inside
cabinets containing the heat-producing electronic
components. A cabinet fan circulates the air across the
heat exchanger and to the heat source in an airtight
circuit. In the coolant-jacket type of heat exchangers,
the distilled water is circulated through an integral water
jacket in a large heat-producing component such as a
power-amplifier tube, a plate transformer, or load
isolators. Vent and drain connections are provided to
permit the venting of trapped air and the draining of
water. Temperature gauges may be provided in the inlet
and outlet piping to check the performance of the heat
exchanger. Label plates indicate the water flow
direction through each cabinet. Flow regulators (orifice
plate or constant-flow device) usually provide a
constant flow of coolant to the individual component,
cabinet, or bay of electronic equipment to be cooled. On
critical electronic components that would be damaged
without coolant to remove the heat, coolant flow and
temperature switches monitor the coolant.
1-9
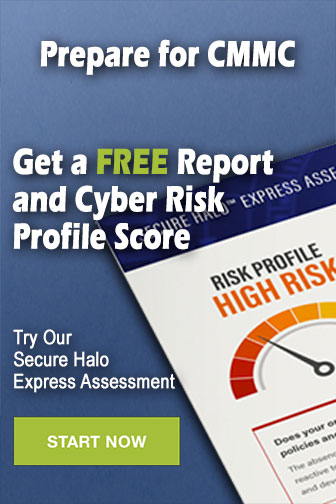