through the tube. The flow restriction is the space
between the float and the tube wall. This area increases
as the float rises.
The differential pressure is fixed depending upon
the weight of the float and the buoyant forces resulting
from the combination of float material and the distilled
waters specific gravity.
The tapered tube of the
rotameter is usually glass with calibration marks reading
directly in gpm. The major advantage of a rotameter
over the venturi orifice meter is the visibility of the
coolant. This allows quick determination of excessive
entrained air in the coolant.
CIRCULATING PUMP
Each cooling system has two secondary distilled
water circulating pumps (fig. 1-24), which are identical
in construction and capacity. One pump is designated
for service, and the other is held in standby in case the
designated pump fails. Should the pump designated for
operation fail, then the standby pump would be used in
its place. The pumps should be operated alternately
(every other week) to prevent deterioration of their shaft
seals, equalize wear, and permit PM actions to be
performed regularly.
The two circulating pumps used in the liquid
cooling system are single-stage centrifugal pumps
closely coupled (pump is built onto the motor) to a
constant-speed electrical motor. You may run into an
older system that uses a separate pump and motor joined
by a flexible coupling. The centrifugal pump has two
major elementsthe impeller rotating on the extension
of the electric motor shaft and a casing that is called the
impeller chamber.
The impeller imparts the initial
velocity to the coolant. The impeller chamber collects
the high-velocity coolant from the impeller and guides
it to the pump outlet. A mechanical shaft seal is used to
eliminate external leakage. This seal is lubricated and
cooled by water ducted from a high-pressure zone of the
pump. You will find a vent valve located on the top of
the pump casing to remove air and ensure the pump is
primed with coolant.
Located at the outlet of each pump is a check valve
to prevent coolant from the outlet side of the operating
pump from circulating to the return side of the coolant
system through the standby pump. Hand-operated
valves at the pumps are used to isolate the pumps so they
can be removed for maintenance.
Each secondary circulating pump is rated in gallons
per minute (gpm) output at a specified head pressure in
pounds-force per square inch gauge (psig) pressure, or
in feet of water. The rating is usually at the pumps
maximum efficiency point, and it will vary depending
upon the pump design. On all pumps, as the output
pressure increases, the output flow decreases, and vice
versa. This relationship is almost linear but differs with
different pump designs. However, this condition means
that if a restriction is placed in the pump output lines,
the pressure will increase and the flow will decrease.
The restriction could be a partially closed hand valve,
dirty filter, damaged or crimped piping or hose, and so
forth. In figures 1-6, 1-7 and 1-8, the pump performance
indicators are the suction and discharge pressure gauges
and the system flowmeter. If you start a pump and
pressure fails to buildup, you should exhaust air through
the vent cock on the top of the pump casing. You should
ensure that the suction valve is fully opened and there is
Figure 1-24.Distllled water circulating pump.
1-19
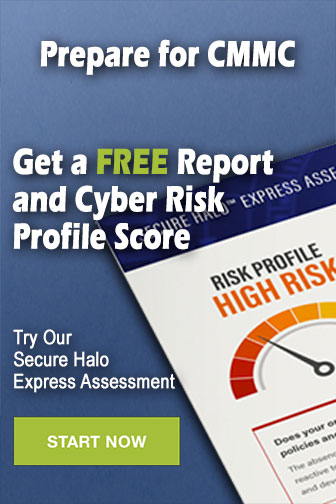