CHAPTER 2
DRY AIR SYSTEMS
For optimum performance of todays transmitting
equipment, especially high-power radar systems and
low-power satellite systems, some rigid coaxial cable
and waveguides are required to be pressurized by air. In
some waveguide systems, dry air is used primarily to
increase the dielectric constant inside the waveguide to
prevent rf energy from arcing inside it. Arcing causes
damage to the inside of the waveguide, and it also
reflects a short circuit back to the power amplifier tube.
As a result, the power tube could sustain major damage.
Also with the use of pressurized dry air, the problems of
corrosion, contamination, collection of moisture, and oil
droplets (which affect preservation) are decreased. At
the same time, the overall reliability of the waveguide
system is increased.
In high-power waveguide runs, the dry air pressure
is approximately 20 to 35 psig. The increased air
pressure increases the dielectric (resistance) strength of
the air. Arcing is then less likely to take place.
In low-power waveguide applications, the dry air is
approximately 1 to 8 psig. The dry air is used primarily
to prevent corrosion and contamination inside the
waveguide. These effects are caused mainly by
moisture in the waveguide.
The number of equipments requiring dry air for
operation has increased drastically in recent years.
Central dry air systems have been installed in many
ships to overcome the problems of individual
maintenance, repair, and supply support required by
individual air dehydrators. There are, however, a large
number of individual equipment dehydrators still in use
on many ships. They are now being used as a back-up
systems should there be a failure in the ships central air
system.
ELECTRONICS DRY AIR
On ships having multiple dry air users, a dedicated
dry air main is installed to support clean, oil free, dry air
to pressurized coaxial cables, waveguides, and other
electronic equipment. Supply to this main is from the
vital main by way of type II or type III dehydrators
installed in parallel so that one serves as a 100 percent
stand-by for the other. In large ships with extensive air
demands, four dehydrators are installed and the air main
can be split for casualty control. The dry air main
terminates at air control panels, which control and
regulate pressure to the electronic user equipment. Four
types of NAVSEA air control panels (type I [user
pressure to 30
type II [user pressure to 60
type III [user pressure of 75
and special [usually
used where pressure flowrate is unused]) are available.
Type I Panels: Typical users URA-38, WRT-1
and WRT-2, SPS-39, ULQ-6, WRL-1, SPS-40
waveguides.
Type II Panels: Typical users SPS-40 cavity,
SPG-51 and SPG-60.
Type III Panels: Typical users require air at 75
to equipment contained regulators such as
SPG-55.
Special: Typical users SPS-32 and SPS-33,
SMQ-10.
In addition, equipment, such as SPS-48 and
SPS-49, are supplied with panels designed for 80 to 125
Each panel is equipped with a sampling
connection, humidity indicator, flow meter, pressure
gauges, and associated valves, to permit the user to
monitor the equipment.
To ensure the reliability of the dry air supply to the
electronic equipment, local dehydrators or local
compressor-dehydrators may be provided. These local
dehydrators are intended for emergency use when battle
damage or casualties result in failure of the central
supply system.
Several methods can be employed to remove excess
moisture from the air. One method is by freezing the air
by means of a refrigerant to remove the moisture. A
second method is to pass the air through a desiccant,
which absorbs the moisture. Some dehydrators use a
combination of both methods to remove moisture from
the air.
2-1
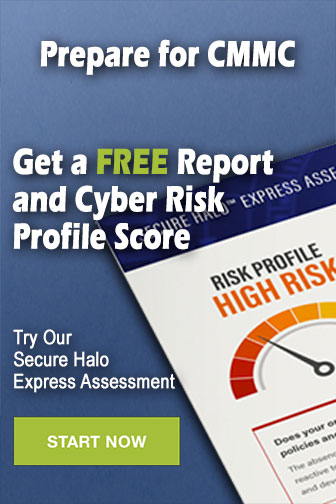